// Detect unfavorable flow patterns at an early stage and optimize your line with the aid of Computational Fluid Dynamics (CFD). ///
Computational Fluid Dynamics (CFD) is an engineering tool that can be used to simulate fluid behavior at any position in a flow field. CFD provides insights into various factors including velocity, pressure, flow direction, temperatures, and many others within a fluid system.
We review and optimize your machine's design and processes during the development stage to ensure the seamless approval of your production process. CFD has the potential to significantly reduce or even entirely replace expensive or time-consuming trials.
We review and optimize your machine's design and processes during the development stage to ensure the seamless approval of your production process. CFD has the potential to significantly reduce or even entirely replace expensive or time-consuming trials.
We can offer you advantages in every phase of your project:
- Verification of process feasibility.
- Layout and design optimization.
- Final machine design validation.
- Acceleration and simplification of the approval process.
- Recipe development and process optimization support.
Laminar Flow Analyse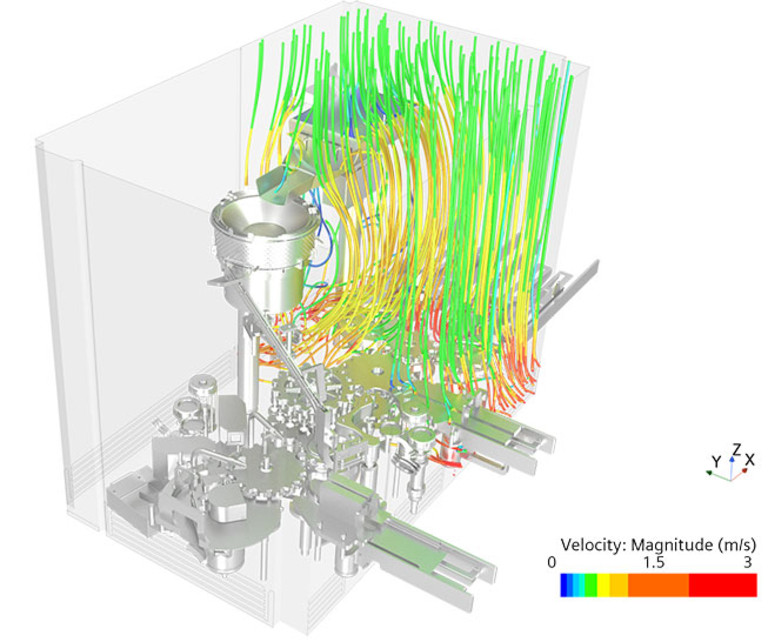
In a laminar flow analysis, we simulate the flow conditions in your production plant under LF equipment. This approach enables us to verify that directional purge flows are in accordance with GMP guidelines.
- Ensure that your equipment complies with GMP standards before starting production.
- Avoid costly and time-consuming design modifications during the FAT/SAT phases.
- Gain a comprehensive overview of the airflow within your production line.
- We will provide you with a comprehensive set of results that you can use as a point of reference in the approval process.
Sterilization Airflow Analyse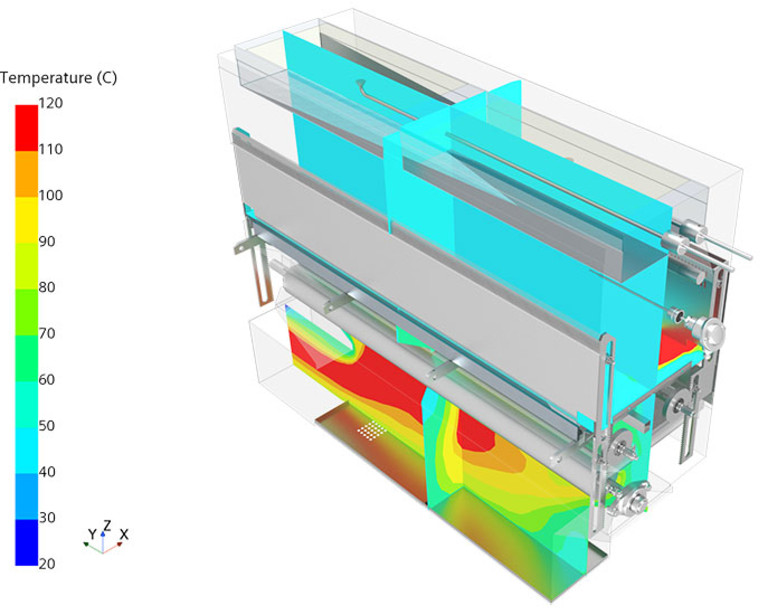
To prevent uneven temperature distribution or failure to reach sterilization temperature in the sterilization tunnel, we can simulate the critical process parameters for you.
Use Sterilization Airflow Analysis to validate your sterilization tunnel. Relying solely on actual trials to achieve this validation can be challenging.
- Optimize and reduce the duration of your energy-intensive heating process.
- Analyze your heating and cooling processes.
Pipe Flow Analyse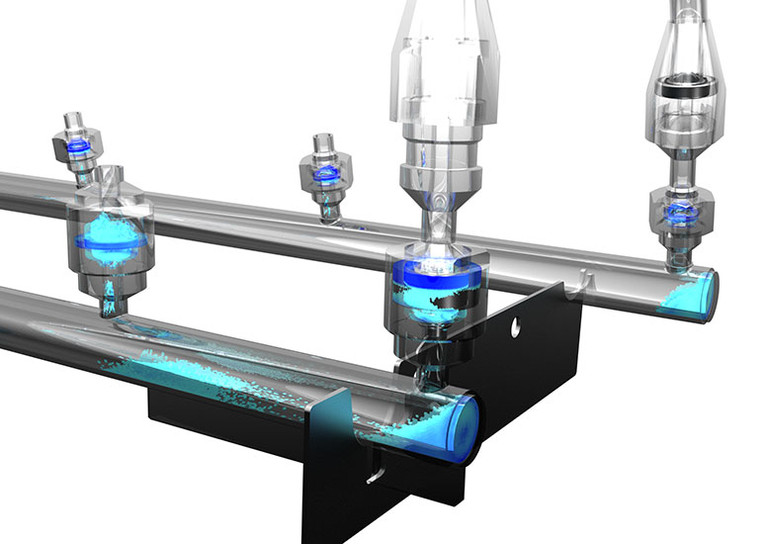
Poorly designed piping systems and incorrectly rated fans or pumps can adversely impact process efficiency. Our simulation software enables us to identify problem zones and to visualize and optimize piping systems in various application areas.
- Validate the design of your piping system.
- Complex, time-sensitive processes can also be accurately mapped.
- You are provided with modification proposals for potential system enhancements.
- Our simulations can be used for a wide range of applications, including product conveyance, cooling circuits, and ventilation systems.
Gas flushing analysis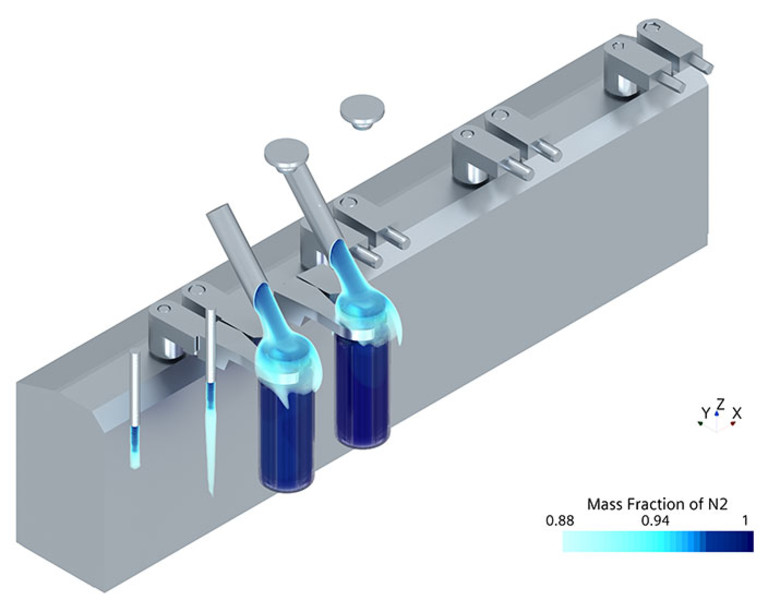
We simulate your gas flushing process to ensure that the residual oxygen content remains below your specified limit when the vial is closed. This not only has the potential to replace expensive and time-consuming real-life tests but also to prevent inefficient nitrogen consumption and reduce cycle times.
- These simulations can be applied to all container types and gas flushing systems.
- Validate your specific gas flushing process.
- Minimize residual oxygen levels in the head space.
Fill analysis
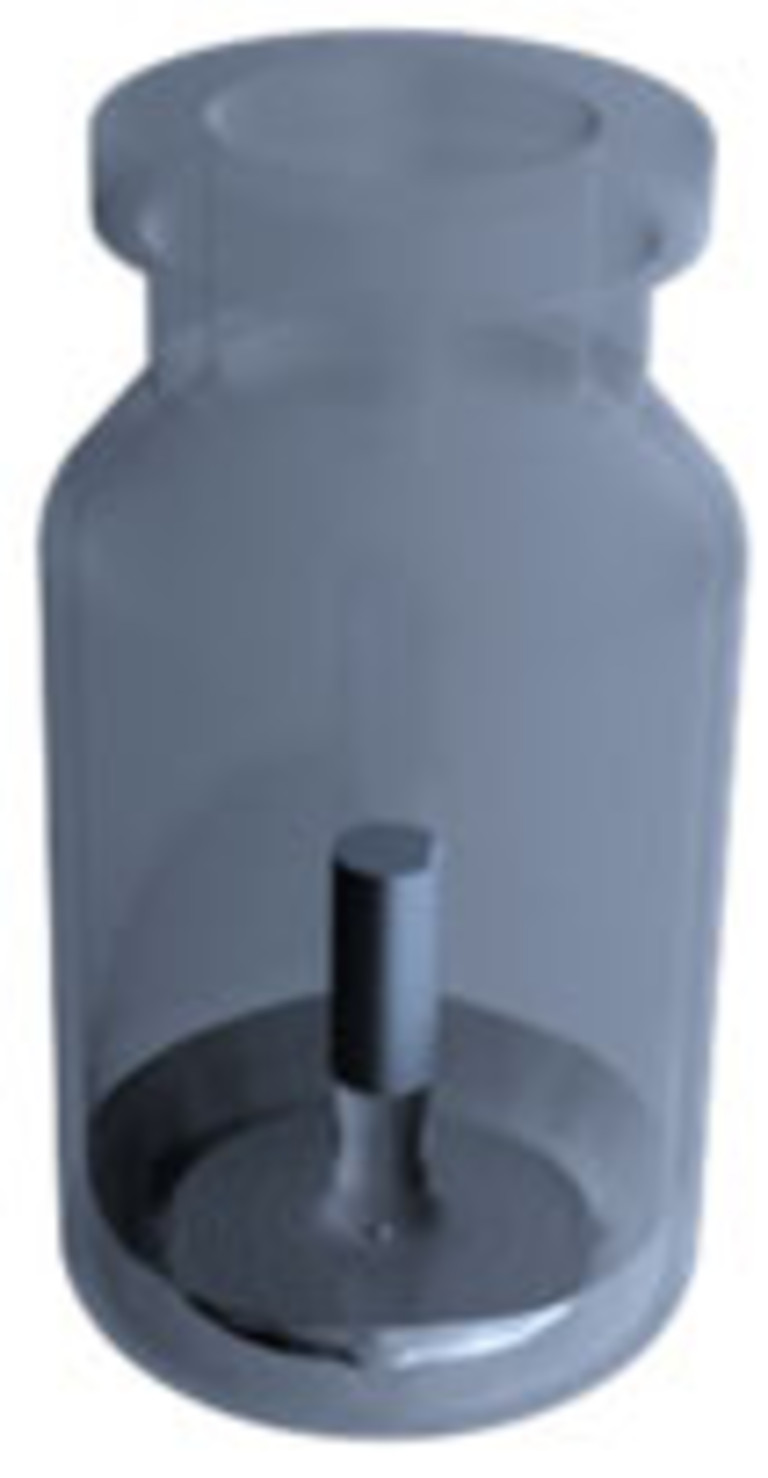
Conducting actual filling trials can consume a significant amount of time and valuable product resources when employed to determine the optimal recipe parameters for a product. Our fill analysis enables you to save time and reduce product loss during recipe development..
- Determining the optimum recipe parameters for a product by means of real filling trials is very time-consuming and involves a considerable waste of valuable product. Our fill analysis saves you time and minimizes product loss during recipe development.
- Through fill analysis, we ensure you achieve a higher level of filling accuracy, regardless of the container being filled.
- Fill analysis optimizes cycle times, enabling you to get the most out of your machine.
- Identify the ideal combination of filling needle and packaging material.
- Minimize costly and time-consuming filling trials.